Ongoing improvements in 3D printing are helping PMI explore new ways to provide engineered solutions that meet customer needs. PMI is improving quality control, prototyping crucial components, and experimenting with designs that will reduce assembly time by taking advantage of 3D printing’s additive manufacturing technology.
“The PMI engineering team has used additive manufacturing to make solid three-dimensional objects from a CAD (computer-aided design) file for several years. Because fabrication materials are improving and becoming more cost-effective, we are investigating more ways we can apply the technology,” says Terrence Mathis, PMI Manager, Engineering-Cable Protection.
Engineering team members are managing small projects to improve mold fabrication, potential part casting, compression dam manufacturing, and more.
Analyzing tolerances and variations to improve quality assurance
PMI is using 3D printing to test engineering tolerances of manufactured parts, such as plugs and rings used in a variety of applications. The time needed to measure internal and external features of parts, and ensure their proper fit, can add hours to the quality control process and affect product yields. Also, it can add time-consuming iterations to production if changes occur late in the design cycle.
“Some complex parts have over 20 features that can take four or more hours to inspect,” Mathis says. “Different tools may be needed to measure each section. Depending on the production quantity, it can add a lot of time. Through tolerance optimization, PMI has the potential to improve manufacturing time and reduce cost.”
Prototyping components that customers need to remain operational
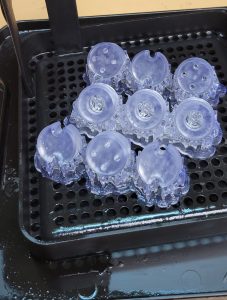
PMI is using 3D printing capabilities to prototype crucial components, such as its precision precast compression dams used in DAM/BLOK™ electrical splice kits.
Many of PMI’s field-installable products incorporate helical gripping rods as part of the kit. At times, it is necessary to reterminate a PMI product—sometimes while out on the ocean–to replace helical rods affected by excessive corrosion, or to refurbish the cable connector.
PMI manufactures the DAM/BLOK™ electrical splice kit as a full-ocean depth pressure splice for cable connections. However, there are over 100 existing DAM/BLOK electrical splice kit designs, not including splice kits that can be custom designed for customers. Despite the degree of customization, each kit includes several crucial components, including precision precast compression dams.
Currently, PMI is testing compression dams to ensure it prevents outside seawater as well as leak water within the cable from passing through the splice to the electrical connection. This is especially important at increasing ocean depths.
Developing designs that reduce assembly time
Customers who purchase PMI’s DYNA II cable hangers benefit from its tool-free installation and multiple degrees of freedom, which allow spreader rope loads to pass through with minimal effect on the lead-in and umbilical cables. Like many PMI products, DYNA II can be custom engineered into several configurable kits and accessories.
A collar assembly is just one of the components in a typical DYNA II configuration. PMI is using 3D printing to develop a new standardized collar to be used on legacy and new systems. The prototype collar is 3D printed in a wax resin, which is then cast in stainless steel. The collar serves a build-measure-learn function while saving tooling costs as PMI works to create an improved collar that benefits its customers.
Thinking outside the box to increase development speed
“Our customers turn to us for engineered solutions that include design, fabrication, and testing of subsea tow cables, hardware, assemblies, and protection,” Mathis says. “With a 3D printer, we’re able to take advantage in low-volume situations to revolutionize our development, design and replacement parts in ways that benefit our customers.”