Terrence Mathis, PMI Mechanical Engineer II, began working for PMI Industries as a part-time project engineer during his last semester at Case Western Reserve University. Terrence was pursuing a mechanical engineering degree and a minor in design and manufacturing. In January, 2017, Terrence joined PMI full time.
Over the years, Terrence has grown and expanded his mechanical engineering expertise within PMI’s team-oriented setting.
“Being part of a small company has allowed me to make an impact in multiple areas, such as sales, production, quality control, and engineering,” he said.
Many PMI customers know of and/or have met Terrence through the engineered protection solutions that he helps develop for customers. We asked Terrence to share more about himself.
What departments have you worked in?
I have always been in the engineering department. I have also helped to support the ISO and quality control (QC) programs periodically.
What machines and materials have you worked with?
Most of my work is done on a computer using CAD (computer-aided design). The program is utilized to help create prototypes and parts used in marine environments. They also help us plan underwater marine cable connector and subsea cable termination projects, store and manipulate data, present information, and more.
I’m proficient in CMM (coordinate measuring machine) programming, which is an important tool used to measure parts for quality control. It’s also been useful in the ways we’re taking advantage of 3D printing’s additive manufacturing technology.
What do you enjoy most about the work you do?
I like being part of a dynamic, involved workplace. We’re a smaller organization, which allows me to build relationships across all departments and feel ‘visible’ in the workplace.
What is a specialty of yours that you are particularly proud of?
I am proud of my CAD skills, which I’ve continued to hone since learning it in college and now use to solve customer problems. The cool part about CAD is that there is always more to learn and many ways to challenge yourself to become more proficient.
At an Offshore Technology Conference, Terrence Mathis, Mechanical Engineer II at PMI Industries, shared his experiences and recommendations as a young professional attending the conference.
How would you describe a “typical” work week?
My work week evolves constantly, depending on many factors, such as customer inquiries, questions about product applications, and the larger, custom projects I oversee. I also support our quality control department with part inspections.
What have you learned about the industry? Are there any trends or changes you are following?
This industry is what we call a niche of a niche. It is expanding quickly, and it is our job to stay up to date with changes so that we can provide high-quality products to our customers. The marine energy industry is expanding and we’re positioning our company to take advantage of this.
I also personally follow the renewable energy sector, especially as it grows in the U.S. A project of interest to me is the Icebreaker Wind Project, which has the potential to become the first freshwater offshore wind farm in Ohio and the U.S.
I am committed to networking. I am a member of National Society of Black Engineers (NSBE), which I originally joined while in college.
When you were a kid, what did you want to be “when you grow up”?
I’ve known that I wanted to be a mechanical engineer since I was 10 years old. I didn’t know what industry I would work in, but the idea of being an engineer has always fascinated me.
When you’re not working, what do you enjoy doing?
I have lived in Cleveland, Ohio, my entire life. My parents and older siblings live here, too. I follow all the Cleveland sports teams and am a big fan of the Cavs and Browns, as well as any team that Lebron James plays for.
Outside of work, I spend a lot of time participating in fitness activities, such as playing basketball with friends or going on runs throughout the city to build up my endurance and stay in shape.
I am also an avid fragrance collector with a large collection of fragrances that I have obtained over the years. Travel, whether by car or flying, is another interest of mine and I am always searching for fund-friendly trips.
Rich Sinkovic, sales engineer at PMI Industries, joined PMI on December 15, 2021. Previously, he had been a sales engineer with a company that produced automotive manufacturing equipment.
In the short time he has been with the company, Rich has gained a lot of knowledge about PMI’s engineered protection solutions for underwater marine cables and subsea cable terminations, including assemblies and hardware that are used in electrical, optical, pressure, and mechanical applications. He has taken what he’s learned about PMI’s underwater marine cable connectors and subsea cable terminations and used it to ensure successful projects for PMI’s customers.
As one of PMI’s newer team members, we asked Rich to share a little about himself.
Please tell us about your education and career path on your way to PMI Industries.
I earned an electrical engineering degree and mathematics minor from Ohio University. For the last 14 years, I have worked as a sales engineer.
What do you enjoy most about the work you do?
Customer interactions are the best part of my work. As I learn about our customers’ projects, I’m able to explain the benefits of our products or services and take their feedback to our engineers and production team.
What is a specialty of yours that you are particularly proud of?
I pride myself on my attention to detail. This helps greatly as I look at costs, lead times, and engineering drawings daily.
How would you describe a “typical” work week?
Typically, I’m working at PMI’s new, state-of-the-art facility, which we moved into in January, 2023. My day is spent communicating with customers via email, phone, and video calls, attending internal meetings to collaborate on new inquiries and new PMI products, and/or researching new markets and opportunities. Often, I visit our lab/production areas to see the progress of production and testing. Occasionally, I travel to visit customers and attend tradeshows and conferences.
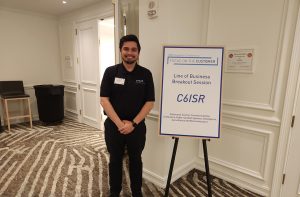
Rich Sinkovic at the Lockheed Martin Rotary & Mission Systems Supplier Conference. PMI is one of Lockheed’s suppliers.
What have you learned about the industry? Are there any trends or changes you are following?
Every project is slightly different, allowing me to continually learn. For instance, one of the markets we work in is seismic and marine surveys. To properly survey, the air guns and streamers need to maintain a certain distance apart from each other. This is accomplished with our Dyna II suspension system.
A recent trend we’ve seen is the move from traditional streamer surveys to node surveys. This reduces the number of streamers needed because the nodes capture the data. We have had many conversations with our customers and designed new Dyna II systems that can handle the larger cables used on node surveys. We plan to follow this closely with our customers and will create new systems as the market requires.
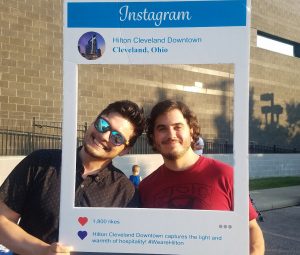
Rich Sinkovic and a friend enjoy live music at City Stages, a summer concert series hosted by the Cleveland Museum of Art at Transformer Station, its satellite location in downtown Cleveland, Ohio.
When you’re not working, what do you enjoy doing?
I live in Lakewood, Ohio, a suburb of Cleveland. I grew up in northeast Ohio and am a Cleveland Browns fan. I like to spend time with family and friends pursuing my interests. For instance, I like to attend live music, go to movies, and search for vinyl records or find new plants to add to my collection. If I’m hanging out at home, I like to read comics and graphic novels, watch TV, or build Lego sets.
When you were a kid, what did you want to be “when you grow up”?
I wanted to work in movies. Not necessarily as an actor, but to be involved in the industry in some capacity.
Experience matters when it comes to ensuring subsea cable systems survive variable ocean conditions. After all, if any part of the cable system assembly fails at sea, repairing or replacing it is expensive and arduous. PMI’s cable testing and analysis is an excellent way for customers and third parties to feel confident about their cable system components and the integrity of the complete system.
“Few labs offer the tests or use the equipment we do to find vulnerabilities and confirm satisfactory performance before the cable is deployed,” says Jay Marino, P.E., PMI Manager, Engineering, Government Services & Test Lab. “We’ve worked with many customers over four decades to simulate at-sea conditions and provide quality inspection and assurance services. PMI’s insight into a product’s durability is a value-added service that customers seek out. They like the fact that our tests can be uniquely tailored to meet their needs.”
As deep ocean exploration has grown over the years, the heavy-duty cables used in subsea projects are expected to last for decades. Unfortunately, 80% of unexpected challenges and delays in marine projects are caused by cable failure.
Equipment provides extensive measurement capabilities
Determining the service life of a cable system and/or its components is a specialty of PMI’s. Besides the tests PMI does on its own products, organizations come to PMI for certification and testing services, particularly ones designed to assess electrical, optical, and mechanical applications.
Customers with new cables may want to do tension cycling on them. PMI’s long span tension setup machine is capable of testing cables up to 457m (1,500 ft.) over multiple sheaves, with tension up to 53.4 kN (12,000 lbf.).
“A manufacturer that makes a cable assembly will send a sample to us to test,” says Marino, who has been involved with PMI’s cable testing facility for over three decades. “Important testing we frequently do for customers checks the cable’s subsea mechanical responses. When someone develops a new cable and wants to run it through its paces, we’ll do tension cycling on it. We’ll also measure the torque and rotation to verify its torque balance characteristics.
“Cables typically are ‘torque balanced,’ but that doesn’t mean they’re perfectly torque balanced,” he continues. “What it means is that the cable is typically designed to minimize torque. Some torque remains, sometimes a little or a lot.
“We can measure the torque that’s generated when it’s loaded. We can also measure its rotation,” he says. “For example, if we fix one end of a cable sample and pull on the other end while allowing it to rotate, we can measure that rotation. Or, we can fix both ends and measure the torque generated in the cable. We can also rotate one end to intentionally generate torque in the sample to see how it reacts. Of course, hydrostatic pressure testing is usually part of the picture. These are tests we typically run. There aren’t many test labs which have this type of equipment.”
The CBOS (cyclic bend over sheave) machine is used to check a cable’s subsea mechanical responses, including its fatigue resistance and simulating its handling system problems.
The equipment PMI uses to test and measure for performance and reliability include:
- Long span tension setup
- Hydrostatic pressure chambers
- CBOS (cyclic bend over sheave) machine
- 100-kip straight tension machine
The equipment can test:
- Raw cable (steel armored or synthetic strength member)
- Rope and hose assemblies
- Cable assemblies
- Cable hardware
- Terminations
- Other equipment used in subsea projects
Customer-driven laboratory testing
One of PMI’s hydrostatic pressure chambers (above) can be used to simulate at-depth pressure loading and verify seal and electrical and optical performance.
Each test is based on the customer’s unique set of parameters. Additionally, the time involved varies based on the customer’s application, interface, and materials requirements.
“We test the cable or component at the conditions that the customer expects during operations in the ocean,” says Thom Bosch, PMI lab technician who has been involved with the company’s laboratory testing for 14 years. “For example, if they’re towing a cable or component through the water, they can calculate the drag force on the towed object, which is related to the tension in the cable. We’ll test to that tension value plus a safety factor for dynamics, usually doing many cycles over hours or days. Our customers typically have an idea of how much variability they can tolerate and still operate their cable system or device.”
These kinds of customer-focused interactions are one reason PMI has been a leader of in-house dynamic cable testing and analysis for nearly 40 years.
The 100-kip straight tension machine is used to measure up to 65 feet of cable to determine its proof, tension and breaking strength.
“We offer independent testing services to any company in the industries we serve,” Marino says. “We can test the performance, and sometimes the limits, of a customer’s cable or equipment beforehand so that there aren’t any expensive surprises in the field.”
To set up a free consultation or get technical support, contact Jay Marino at jmarino@pmiind.com or any member of our leadership or sales team. Their contact information is found on the Contact Us page on our website.
In case you missed it, we’ve moved–and the PMI team is settled into our new home!
Housed at our previous facility since PMI’s inception in 1984, it was time for an upgrade. We’re now located at 990 Resource Drive, Cleveland, Ohio 44131, U.S.A., just 7 miles away from the old facility.
The new state-of-the-art facility provides increased production and testing space, improves process flow, and allows for the growth of customized cable engineering solutions.
“By moving to the new facility, we’re able to better meet the needs and requirements of our customers,” said Bob Centa, President. “For instance, our production flow is better suited to meet the trends in the industries we serve, improving productivity and efficiency in handing large cable reels.”
Other benefits of the new facility include:
- Expansion of PMI’s design, manufacturing, and testing capabilities that will dramatically improve operational efficiencies.
- Increase product and service offerings to PMI’s customers.
- Expand PMI’s geographic reach.
We’re excited about this new chapter and we’d love to share a bit of the transition to our new space with you through the pictures below.
We are proud to announce that after an external audit, the Quality Management System of PMI Industries, Inc. has been assessed and approved by Smithers Quality Assessments, Inc., to the following quality management system standard and requirements: ISO 9001:2015.
This certifies that our Quality Management System is applicable to design, manufacture and distribute offshore, subsea cable hardware assemblies, and provide testing services. Which demonstrates our commitment to our Quality Policy Statement:
PMI Industries, Inc. provides offshore, subsea cable hardware and assemblies that increase efficiency, reduce failures, and improve installation and deployment time. We are committed to meeting customer expectations, and all applicable requirements, through continuous improvement of our processes. Our advantage is delivering quality, on-time and cost-effective products and services.
Since 2017, PMI has partnered with Smithers Quality Assessments, an accredited quality and environmental management systems certification body, to achieve certification.
“This certification reflects our longstanding commitment to quality, continuous improvement, and our customers,” said Bob Centa, President of PMI Industries, Inc. “It demonstrates the significant effort by the PMI team to continue to uphold the ISO standard throughout the company.”
PMI, celebrating a history of 39 years in 2023, is a global leader in engineered solutions for underwater marine cable connectors and terminations, including assemblies and hardware. The solutions that PMI designs, manufactures, and tests are used on cable systems for impact and abrasion protection, to prevent bending and provide strain relief, and for dynamic and static cable protection.
Our products include high-strength cable terminations and gripping products, towed array and seismic survey lead-in and umbilical terminations, and suspension cable assemblies and hardware.
Our engineered subsea cable hardware assemblies are designed for the following:
- US Navy & Defense Contractors
- Oil & Gas
- Marine & Seismic Survey
- Ocean Exploration & Research
- Offshore Wind, Wave, and Tidal
- University and Research Institutes