As Sales Coordinator at PMI Industries, Tijana Milev plays a pivotal role at the heart of customer communication, often serving as the first and last point of contact for clients. With a background in technical industries and multilingual communication, she brings a unique blend of cultural understanding, professionalism, and warmth to every interaction.
“I like to leave people better than I found them,” Tijana says. “It’s much more than a sales transaction. It’s about making a positive impact, going above and beyond, and ensuring our customers feel valued.”
A Collaborative Force Within PMI
Tijana joined PMI in June 2021, drawn by the company’s manufacturing capabilities, collaborative culture, and strong reputation for quality. Her passion for teamwork is clear. “Sales at PMI is deeply connected to every department, from engineering and production to shipping,” she explains. “We’re all aligned to deliver the best possible solution.”
That spirit has made a difference on many projects, including the development of a custom Fiber Optic Splice Kit. “The specifications were ever-changing, and the timeline was tight. It required constant communication and flexibility. It was a true team effort.”
Sales with Purpose: Creating Meaningful Customer ExperiencesFor Tijana, sales is more than closing deals; it’s about creating a thoughtful, white-glove experience, especially with global clients. As PMI expands internationally, her ability to speak multiple languages and connect across cultures is a major asset.
“I was told a long time ago, the more languages you know, the more valuable you are to the world,” she shares. “Growing up multilingual helped me develop an ear for accents and, more importantly, a deep appreciation for other cultures. I make it a point to listen first, communicate intentionally, and build real relationships.”
She adds, “Sometimes it’s as simple as picking up the phone. In our email-heavy world, just calling someone, asking how they’re doing, even what the weather’s like, makes a big impression. It shows effort, care, and humanity.”
Driving Sales & Marketing Impact
Beyond her coordination work, Tijana supports PMI’s Sales & Marketing efforts, helping craft messaging, develop customer materials, and drive outreach across channels. Her insights help shape how PMI presents its solutions to the world.
“I love being involved in both the execution and the story behind what we do,” she says. “It’s not just about answering sales inquiries. It’s about understanding our capabilities, sharing them in a compelling way, and reaching the right people.” Whether behind the scenes or representing PMI at events, Tijana connects the product, the brand, and the people it serves.
Representing PMI on the International Stage
That care and connection shine on the global stage, including at events like the recent EAGE Annual Conference in France and the upcoming IMAGE in Houston, where PMI engages with clients and partners worldwide.
Tijana looks forward to reconnecting with long-time customers, especially from Japan and Norway. “They recognize the quality of our product and the consistency of our service. We’ve built trust over time. These face-to-face moments at events reinforce that trust and show we’re invested in their success.”

Tijana Milev representing PMI Industries at the IMAGE 2024 Conference, connecting with international clients & partners.
Belief in the Product & the People Behind It
Tijana takes pride in PMI’s commitment to quality. “We’re known for the durability and reliability of our products, and I truly believe in what we do. Seeing our test lab in action and the rigor our products go through gives me even more confidence when speaking to clients.”
That belief extends to her colleagues. “Our team is dynamic, talented, and collaborative. We support each other, we innovate together, and we care about the outcomes.”
Growth & Looking Ahead
Since joining PMI, Tijana has contributed to major Sales & Marketing milestones — from refreshing the company’s brand and website to launching new products and improving internal processes. For her, success is about continuous learning, creative problem-solving, and impact.
As PMI grows its global reach, Tijana is excited for what’s ahead. Whether supporting long-time clients or guiding new ones through their first project, she remains focused on what matters most: providing exceptional service, building trusted relationships, and being someone the team can rely on.
“I want to be someone my teammates and our customers can count on,” she says. “That’s what makes the work meaningful.”
Please join us in recognizing Tijana Milev for the important role she plays in helping PMI deliver high-quality, solutions-based service across the globe.
At PMI Industries, we recognize that a strong supply chain is the backbone of our operations. As we bid farewell to longtime Supply Chain Manager Hany Koury, who is retiring this year, we are excited to introduce Chris Calvert as his successor. With a deep commitment to quality, strong leadership, and a passion for building meaningful relationships, Chris is poised to continue PMI’s legacy of excellence in Supply Chain Management.
A Career Built on Quality and Excellence
Chris joined PMI Industries in July 2023, bringing with him nearly a decade of experience from one of the largest aerospace manufacturing facilities in the United States. His background in quality control and dedication to operational excellence made him a perfect fit for PMI’s customer-focused and high-standards-driven environment.
“Quality has always been a cornerstone of my professional approach,” Chris shares. “It’s the foundation of any successful organization.”
Chris began his journey at PMI as a Quality Control Inspector, where his keen attention to detail and commitment to high standards quickly made an impact. His leadership skills and deep understanding of operational processes led to his promotion to Supply Chain Manager. In this role, he plans to apply the same meticulous approach to ensuring PMI’s Supply Chain remains efficient, reliable, and aligned with our company’s mission.
Commitment to Growth and Education
Recognizing the importance of continuous learning, Chris is currently pursuing an Associate of Science in Business Administration at Southern New Hampshire University, with plans to graduate in May 2025. He intends to continue his education with a Bachelor’s degree, further strengthening his knowledge of Supply Chain Management.
“I was looking for a company that aligned with my values, and PMI has been that place for me,” he explains. “The family-oriented environment here makes me excited about my future with the company.”
A Strategic Approach to Supply Chain Management
In his role as Supply Chain Manager, Chris oversees critical functions such as Procurement, Inventory Management, and Vendor Relations. His daily responsibilities include:
- Ordering materials for new sales orders to ensure seamless production.
- Collaborating with the Shipping Department to maintain PMI’s reputation for on-time deliveries.
- Ensuring inventory accuracy and cost-effective pricing with the Sales Team.
- Assisting colleagues across departments to maintain a strong team environment.
Chris takes great pride in optimizing processes and driving efficiencies. One of his key accomplishments has been programming PMI’s coordinate-measuring machine (CMM) to develop tailored programs for machined products. This advancement has significantly improved quality control and streamlined production.
Building Strong Relationships
Chris is particularly passionate about forging strong relationships with vendors and customers. He understands that these partnerships are essential to PMI’s continued success and strives to build trust and collaboration across all touchpoints.
“What I enjoy most about my work is the opportunity to connect with people,” he says. “Building positive, long-term relationships with vendors and customers creates lasting success for everyone involved.”
A Family-Oriented Leader
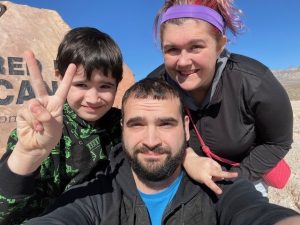
Chris enjoying an outdoor adventure with his wife and son—cherishing quality time before welcoming their new addition in June.
When he’s not working, Chris dedicates his time to his family. He and his wife celebrated 10 years of marriage this February, and they’ve been together since their freshman year of high school. They have a 10-year-old son and are excited to welcome another baby boy this June!
“Everything I do is for my family,” Chris shares. “They are my greatest motivation.”
Beyond family time, Chris enjoys playing video games with friends, traveling, and playing the guitar—an instrument he’s loved since he was six years old.
Looking to the Future
Although Chris once dreamed of becoming a police officer as a child, he is grateful for the path that led him to PMI Industries. His dedication, expertise, and leadership make him an invaluable addition to the team, ensuring that PMI’s Supply Chain Operations remain in capable hands.
Please join us in welcoming Chris Calvert as PMI’s Supply Chain Manager. We are confident that his expertise and passion will continue to drive our company’s success for years to come!
When Hany Koury, PMI Industries Supply Chain Manager, graduated from the American University in Cairo, Egypt, he planned to become a fighter pilot in the U.S Air Force (USAF). A chance meeting changed his plans, however.
He was offered a great opportunity to work with a global aerospace and defense company, which was starting to deploy its F-16 Fighting Falcon fighter aircraft to Egypt. The person who recruited him said they needed someone with Hany’s unique skills, conversant in multiple languages and knowledgeable in computer science, to help manage logistics. Hany accepted the challenge.
For nearly two decades, Hany remained in the Middle East before moving to the U.S. to live near his mom and relatives in northeast Ohio. Hany, who previously had only worked for large, multinational corporations in start-up mode in Egypt, decided to take an inventory control position at a small, family-run business. He liked the atmosphere immediately, especially seeing the direct results of his suggestions and effort.
A few years later, Hany began looking for a new challenge and found a supply chain management opportunity at PMI Industries. He applied and was hired to join PMI’s family-run team.
“I felt how strong family was here,” Hany said. “Bob Eucker and Allan Metzler, who started PMI and worked here until they retired, treated me as part of the family from Day 1.”
Since 2008, Hany has had a front row seat to PMI Industries’ growth as a global leader in engineered protection solutions for underwater marine cable connectors and subsea cable terminations. Now, after 17 years at PMI, Hany plans to retire later this year.
Hany, an avid sailor, has a fresh challenge awaiting him. He and his wife will sail their 40-foot sailboat through the Erie Canal to the Hudson River and along the East Coast. They plan to make Oriental, NC, their home port, visiting family in Ohio periodically.
Have you always worked in the same department and role?
I’ve always worked as a supply chain manager. PMI was very small when I started. We worked mostly with the U.S. Department of Defense. Our DYNA hanger system was just starting up. That is what really launched PMI. After this product was introduced, PMI’s reputation skyrocketed.
What gave you the most satisfaction at work?
Being part of this company and watching it grow, especially internationally. I consider PMI to be one of the top underwater cable solutions providers in the world, thanks in part to our engineers and products.
I worked alongside great engineers like Frank Albert, the PMI engineer who earned several patents and designed several products, including what is known as the EVERFLEX™ BSR Bending Strain Relief product; Bill Green; Konstantin Nakovski, and Jay Marino, P.E., PMI Manager, Engineering, Government Services and Test Lab. They developed amazing products, including the Dyna II® family, a product line that is changeable, adjustable, and reliable. Reliability at sea is a big deal. We have people on ships who specifically ask for our products.
What have your biggest contributions been while here?
My contribution has been to find sources and suppliers. I work closely with our sales, engineering, and operations departments to determine demand requirements, develop action plans to cover supply gaps, and procure manufacturing supplies to be used on the production floor and lab areas.
What are the most significant changes that you have noticed at PMI Industries since you started here?
The way we define ourselves. We’re not a manufacturing company. We are an engineering company that makes solutions. We make a part to solve a customer’s order to their specifications. Plus, we’re able to design, manufacture, and test in a state-of-the-art facility that provides increased production and testing space.
When you were a kid, what did you want to be “when you grow up”?
I wanted to be a fighter pilot in the US Air Force. That opportunity never happened but I was still able to become a recreational pilot and fly gliders with and without motors. One of my favorite hobbies is operating remote-controlled airplanes and sailboats.
Do you have any advice for people just starting at PMI Industries?
Work hard and dream big. This is an amazing company to work for.
There are still communities in the United States without internet infrastructure. Now a Brooklyn Heights company is making connections to solve that problem.
Read the entire story on WKYC.
FOR IMMEDIATE RELEASE
Split Marine-Grade, Stainless Steel for ease of handling and simplified installation.
Cleveland, OH, USA, August 29, 2024 – PMI Industries, Inc., a global leader in engineered solutions for underwater marine cable connectors and subsea cable terminations introduces the Fiber Optic Splice Kit. The innovative kit ensures a waterproof splice while terminating each end of the cable, making it secure even in the harshest environments. The Fiber Optic Splice Kit can be installed anywhere along the cable to create a highly reliable, full ocean-depth splice with multiple levels of sealing protection. PMI’s splice kit enclosure family of products is specialized to each customer’s application.
Power & Tel, a trusted distributor of communications equipment based in Memphis, Tennessee, with a 60-year history, recently employed the Fiber Optic Splice Kit for a unique application “I am truly impressed with the level of product quality and attention to detail. Every aspect of their product reflects a commitment to excellence, from the meticulous design elements to the flawless execution,” comments Tom James, Director. “What truly sets them apart, however, is their exceptional customer service. They went above and beyond to ensure our needs were met and exceeded our expectations in every way.”
Jim Boone, PMI’s Vice President, added, “We were presented with a unique project by a new customer to develop and produce a specialized fiber optic underwater splice kit. With a tight timeline, it was an all-hands effort by our engineering, sales, and supply chain management teams. By leveraging our design engineers’ knowledge and in-house testing capabilities, we were able to validate the new design and exceed the customers’ requirements.”
Bob Centa, President / CEO of PMI said, “The Fiber Optic Splice Kit is a perfect example of what PMI excels at– our team worked closely with the customer and our suppliers to ensure high quality and performance and timely delivery.” (Photo attached).
About PMI Industries, Inc.
PMI, celebrating 40 years in 2024, is a global leader in engineered protection solutions for underwater marine cable connectors and subsea cable terminations, including assemblies and hardware that are used in electrical, optical, pressure, and mechanical applications. The solutions that PMI designs, manufactures, and tests are used on cable systems for impact and abrasion protection, to prevent bending and provide strain relief, and for dynamic and static cable protection. Its products include high-strength cable terminations and gripping products, towed array and seismic survey lead-in and umbilical terminations, and cable assemblies and hardware. Markets served include U.S. Navy & defense contractors; oil & gas/seismic survey; ocean (marine) exploration/university & research institutes; and communications. For additional information, visit www.pmiind.com.
Media Contact: Robert Felber
Felber PR & Marketing
(330) 963-3664, RobFelber@FelberPR.com
# # #
Certification requires rigorous audit process by the US Navy’s Submarine Maintenance Engineering, Planning and Procurement (SUBMEPP)
Cleveland, OH, USA, May 08, 2024 – PMI Industries, Inc., a global leader in engineered solutions for underwater marine cable connectors and subsea cable terminations, recently earned the prestigious certification as a NAVSEA S9320-AM-PRO-020 approved molding facility from the U.S. Navy’s Submarine Maintenance Engineering, Planning and Procurement (SUBMEPP). By achieving this highly sought-after qualification, PMI is one of only a handful of companies in the country with the NAVSEA S9320-AM-PRO-020/MLDG certification. As a result, PMI is now an approved vendor to fabricate, mold, and inspect outboard cable assemblies and components for the U.S. Navy.
The approval process required a rigorous audit by SUBMEPP, which performs life cycle maintenance and modernization planning for the U.S. Navy nuclear submarine fleet. During the audit, PMI’s cable assemblies and terminations, along with its quality assurance team, demonstrated adherence to the exacting standards and specifications outlined in the NAVSEA Technical Manual.
The certification opens other opportunities for PMI, an ISO 9001:2015 with Design certified global leader in the design and manufacturing of high-performance, custom, and to-print cable assemblies and cable protection hardware.
“We are proud to be approved as a NAVSEA S9320-AM-PRO-020 molding facility by the U.S. Navy,” said Bob Centa, President & CEO. “Achieving the NAVSEA certification as a molding facility showcases our continuing commitment to providing highly reliable assemblies to the Navy. As we start our 5th decade in business, we will continue to design, engineer, and build dependable solutions for our customers operating in harsh environments around the world.
About PMI Industries, Inc.
PMI, celebrating 40 years in 2024, is a global leader in engineered protection solutions for underwater marine cable connectors and subsea cable terminations, including assemblies and hardware that are used in electrical, optical, pressure and mechanical applications. The solutions that PMI designs, manufactures and tests are used on cable systems for impact and abrasion protection, to prevent bending and provide strain relief, and for dynamic and static cable protection. Its products include high-strength cable terminations and gripping products, towed array and seismic survey lead-in and umbilical terminations, and cable assemblies and hardware. Markets served include U.S. Navy & defense contractors; oil & gas/seismic survey; ocean (marine) exploration/university & research institutes; and renewable energy. For additional information, visit www.pmiind.com.
Michelle Kane, mechanical engineer at PMI, was born and raised in northeast Ohio. She stayed in the region to attend Cleveland State University, which offered a 4+1 program. That program enabled Michelle to earn a bachelor’s and master’s degree in mechanical engineering in five academic years instead of six.
After college, Michelle worked at a temperature sensor company in Mansfield. Midway through the global pandemic, however, Michelle decided that she preferred employment closer to her family. Michelle’s job search led her to PMI, which she joined in April, 2022.
“I enjoy the variety in my day-to-day work,” she said. “I work in the engineering department and am involved with many different projects and all our departments. The environment is fast-paced and I’m always learning something new.”
We asked Michelle to share more about herself and the work she does at PMI.
What machines and materials have you worked with?
I often work on projects that involve 3D printing and the use of an autoclave. We use the autoclave to replicate ocean depth and for pressure testing.
What is a specialty of yours that you are particularly proud of?
Being organized. I manage multiple projects, as well as PMI’s ISO and safety programs. I use weekly to-do lists to keep track of what needs to be done.
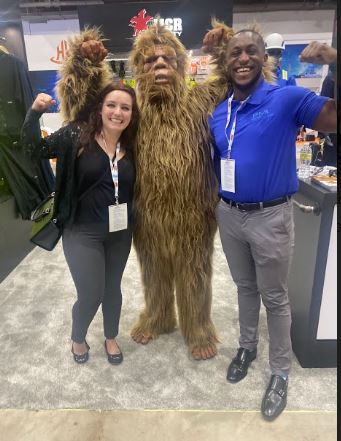
PMI Industries’ Michelle Kane and Terrence Mathis meet Sasquatch, also known as Bigfoot, at the Offshore Technology Conference (OTC). For the PMI team, attending trade shows are one way it fosters and builds customer relationships.
How would you describe a “typical” work week?
A typical work week for me involves working with a variety of departments and people inside and outside of the company. For instance, I provide project information and updates on customer interaction to our sales team. With the production team, the focus is on work orders, procedures, testing, and training. In our quality control, supply chain, and shipping and receiving areas, my involvement ranges from parts to be ordered or evaluated to products shipped to customers or vendors. In my ISO role, I work with all our departments to collect data for key performance indicators, which are used to update and improve procedures and processes and/or create new guidance documents as needed.
What have you learned about the industry? Are there any trends or changes you are following?
I didn’t know just how specialized PMI’s business was when I joined 19 months ago. I have learned so much about vessels, surveys, remote-operated vehicles, fiber optics, etc. and the solutions that PMI designs, manufactures, and tests. At PMI, I’m assisting or leading projects and get to be directly involved with our products, such as our new fiber optic splice kit, Dyna II family, EVERFLEX™ BSR Bending Strain Relief, DAM/BLOK™ Electrical Cable Splice Kit, and other marine cable connectors and subsea cable terminations.
One group I follow on social media is called, “Interesting Engineering.” It has been posting about fiber optics and fiber optic cables and the alternate ways they are being used. One example mentioned using fiber optic cables to track whales using seismographs. Interestingly, PMI’s solutions are assisting in this offshore work and data collection of whale songs!
When you’re not working, what do you enjoy doing?
Northeast Ohio has a huge volleyball community. I am part of this and play volleyball about five days a week. I also enjoy reading novels and manga, watching anime and TV shows, going to concerts, and spending time with friends, family, and my three cats.
When you were a kid, what did you want to be “when you grow up”?
I wanted to do special FX makeup, either for movies or plays. I began studying chemical engineering to “make” makeup. That’s when I discovered how much I despise chemistry! I switched to mechanical engineering after two semesters of general chemistry in my freshman year of college.
By Bob Centa, President of PMI Industries
The start of a new year is a wonderful opportunity to express appreciation, reflect on past accomplishments, and look forward to the future. At PMI Industries, we have many reasons to be proud of the work we are doing and the value and opportunities this creates for our key stakeholders.
Our business provides engineered protection solutions for underwater marine cable connectors and subsea cable terminations, including assemblies and hardware that are used in electrical, optical, pressure, and mechanical applications. The solutions we create enable us to service customers around the world through the four different markets in which we operate. We look forward to building upon the strength of these relationships as we embark on our 40th year in business.
Acknowledging PMI’s relationships
PMI’s key stakeholders include our shareholders, employees, suppliers, and customers. We appreciate our shareholders, who provide support when needed and the autonomy to think and act for the long-term health and growth of the business. We are thankful for our employees, who embody a “can-do” attitude and deserve thanks because of the ways in which they embrace new opportunities presented by our customers and help us meet daily operational challenges. We are indebted to our suppliers for their critical inputs, helping us meet the needs of our customers and/or our own operations.
We are grateful to our customers, many of which have done business with PMI for decades. Whether old or new, our customers can count on our subsea cable engineering experts to design, manufacture, and test cable systems for impact and abrasion protection, to prevent bending and provide strain relief, and for dynamic and static cable protection.
Gaining momentum in 2023
We made improvements and changes in 2023 designed to better serve our customers and position us for growth. Among our biggest accomplishments were:
- Facilities upgrade – PMI relocated to a larger, state-of-the-art facility early in 2023. The new space allows us to better address customers’ needs and requirements through operational efficiencies and improved manufacturing and testing processes. The facility offers added bonuses, which include:
- Activating sustainable manufacturing processes that conserve energy and natural resources, such as LED lighting
- Improving ingress and egress for our customers and suppliers
- Positively impacting employee retention and recruitment
- Our people – Key additions in engineering, quality control, accounting, and production were made to an already dedicated team. Each member of the PMI team is making significant contributions to meet, and exceed, our customers’ expectations. You can meet two of them, Rich Sinkovic and Terrence Mathis, who were featured in recent stories on our website and social media.
- New products – A customer referral brought together our sales, engineering, supply chain, production, and quality control teams to provide a solution to a new challenge. The PMI team did an outstanding job in satisfying the customer and exceeding their requirements. Additionally, this product has the potential to cross over into many other applications. The project was a perfect example of PMI at its finest in terms of how we meet the unique needs of our customers, despite significant challenges.
- Our services – We took the opportunity to better communicate the extensive testing capabilities we offer. With the growth in the diameter of and materials used in cables, we have been reminding customers and interested cable manufacturers about PMI’s in-house dynamic cable testing and analysis. It provides an extra confidence boost with their cable system components and the integrity of the complete system.
- New markets – We successfully completed production of a new renewable energy product and collaborated with the customer during installation. As the world seeks alternatives to meet global energy needs, PMI is excited about the growth prospects this market offers.
- Improved communications – Significant enhancements made to our website and social medial channels have made them more informative and user friendly. We are regularly updating our LinkedIn and X (formerly Twitter) accounts with interesting content and encourage you to check it out.
Building new opportunities in 2024
We are excited about what 2024 holds. We enter the year leveraging our solid foundation, which allows us to better meet the needs of our customers and deliver existing products while creating new ones in the markets we serve.
Two key areas on which PMI is focused in 2024 are:
- Customer and supplier engagement – While we realize the world has changed due to the global pandemic, we feel strongly about the importance of relationships. We remain committed to meeting customers and suppliers whenever possible, whether at trade shows, their place of business, or anywhere else in the world.
- Processes – With the core infrastructure firmly in place, our last big initiative is the replacement of our Enterprise Resource Planning (ERP) systems. Replacing our ERP system is not just an update; it’s a strategic move towards future-proofing our business operations, enhancing efficiency, and maintaining our competitive edge in the market.
We would love to hear from you. Please contact us if you have any questions or if there is anything we can do for you.
Terrence Mathis, PMI Mechanical Engineer II, began working for PMI Industries as a part-time project engineer during his last semester at Case Western Reserve University. Terrence was pursuing a mechanical engineering degree and a minor in design and manufacturing. In January, 2017, Terrence joined PMI full time.
Over the years, Terrence has grown and expanded his mechanical engineering expertise within PMI’s team-oriented setting.
“Being part of a small company has allowed me to make an impact in multiple areas, such as sales, production, quality control, and engineering,” he said.
Many PMI customers know of and/or have met Terrence through the engineered protection solutions that he helps develop for customers. We asked Terrence to share more about himself.
What departments have you worked in?
I have always been in the engineering department. I have also helped to support the ISO and quality control (QC) programs periodically.
What machines and materials have you worked with?
Most of my work is done on a computer using CAD (computer-aided design). The program is utilized to help create prototypes and parts used in marine environments. They also help us plan underwater marine cable connector and subsea cable termination projects, store and manipulate data, present information, and more.
I’m proficient in CMM (coordinate measuring machine) programming, which is an important tool used to measure parts for quality control. It’s also been useful in the ways we’re taking advantage of 3D printing’s additive manufacturing technology.
What do you enjoy most about the work you do?
I like being part of a dynamic, involved workplace. We’re a smaller organization, which allows me to build relationships across all departments and feel ‘visible’ in the workplace.
What is a specialty of yours that you are particularly proud of?
I am proud of my CAD skills, which I’ve continued to hone since learning it in college and now use to solve customer problems. The cool part about CAD is that there is always more to learn and many ways to challenge yourself to become more proficient.
At an Offshore Technology Conference, Terrence Mathis, Mechanical Engineer II at PMI Industries, shared his experiences and recommendations as a young professional attending the conference.
How would you describe a “typical” work week?
My work week evolves constantly, depending on many factors, such as customer inquiries, questions about product applications, and the larger, custom projects I oversee. I also support our quality control department with part inspections.
What have you learned about the industry? Are there any trends or changes you are following?
This industry is what we call a niche of a niche. It is expanding quickly, and it is our job to stay up to date with changes so that we can provide high-quality products to our customers. The marine energy industry is expanding and we’re positioning our company to take advantage of this.
I also personally follow the renewable energy sector, especially as it grows in the U.S. A project of interest to me is the Icebreaker Wind Project, which has the potential to become the first freshwater offshore wind farm in Ohio and the U.S.
I am committed to networking. I am a member of National Society of Black Engineers (NSBE), which I originally joined while in college.
When you were a kid, what did you want to be “when you grow up”?
I’ve known that I wanted to be a mechanical engineer since I was 10 years old. I didn’t know what industry I would work in, but the idea of being an engineer has always fascinated me.
When you’re not working, what do you enjoy doing?
I have lived in Cleveland, Ohio, my entire life. My parents and older siblings live here, too. I follow all the Cleveland sports teams and am a big fan of the Cavs and Browns, as well as any team that Lebron James plays for.
Outside of work, I spend a lot of time participating in fitness activities, such as playing basketball with friends or going on runs throughout the city to build up my endurance and stay in shape.
I am also an avid fragrance collector with a large collection of fragrances that I have obtained over the years. Travel, whether by car or flying, is another interest of mine and I am always searching for fund-friendly trips.
Rich Sinkovic, sales engineer at PMI Industries, joined PMI on December 15, 2021. Previously, he had been a sales engineer with a company that produced automotive manufacturing equipment.
In the short time he has been with the company, Rich has gained a lot of knowledge about PMI’s engineered protection solutions for underwater marine cables and subsea cable terminations, including assemblies and hardware that are used in electrical, optical, pressure, and mechanical applications. He has taken what he’s learned about PMI’s underwater marine cable connectors and subsea cable terminations and used it to ensure successful projects for PMI’s customers.
As one of PMI’s newer team members, we asked Rich to share a little about himself.
Please tell us about your education and career path on your way to PMI Industries.
I earned an electrical engineering degree and mathematics minor from Ohio University. For the last 14 years, I have worked as a sales engineer.
What do you enjoy most about the work you do?
Customer interactions are the best part of my work. As I learn about our customers’ projects, I’m able to explain the benefits of our products or services and take their feedback to our engineers and production team.
What is a specialty of yours that you are particularly proud of?
I pride myself on my attention to detail. This helps greatly as I look at costs, lead times, and engineering drawings daily.
How would you describe a “typical” work week?
Typically, I’m working at PMI’s new, state-of-the-art facility, which we moved into in January, 2023. My day is spent communicating with customers via email, phone, and video calls, attending internal meetings to collaborate on new inquiries and new PMI products, and/or researching new markets and opportunities. Often, I visit our lab/production areas to see the progress of production and testing. Occasionally, I travel to visit customers and attend tradeshows and conferences.
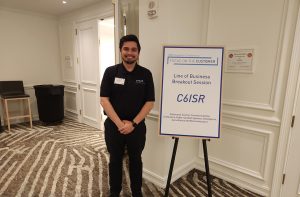
Rich Sinkovic at the Lockheed Martin Rotary & Mission Systems Supplier Conference. PMI is one of Lockheed’s suppliers.
What have you learned about the industry? Are there any trends or changes you are following?
Every project is slightly different, allowing me to continually learn. For instance, one of the markets we work in is seismic and marine surveys. To properly survey, the air guns and streamers need to maintain a certain distance apart from each other. This is accomplished with our Dyna II suspension system.
A recent trend we’ve seen is the move from traditional streamer surveys to node surveys. This reduces the number of streamers needed because the nodes capture the data. We have had many conversations with our customers and designed new Dyna II systems that can handle the larger cables used on node surveys. We plan to follow this closely with our customers and will create new systems as the market requires.
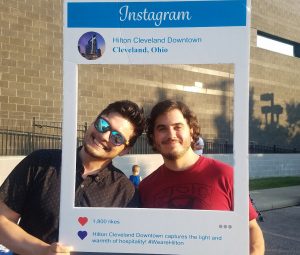
Rich Sinkovic and a friend enjoy live music at City Stages, a summer concert series hosted by the Cleveland Museum of Art at Transformer Station, its satellite location in downtown Cleveland, Ohio.
When you’re not working, what do you enjoy doing?
I live in Lakewood, Ohio, a suburb of Cleveland. I grew up in northeast Ohio and am a Cleveland Browns fan. I like to spend time with family and friends pursuing my interests. For instance, I like to attend live music, go to movies, and search for vinyl records or find new plants to add to my collection. If I’m hanging out at home, I like to read comics and graphic novels, watch TV, or build Lego sets.
When you were a kid, what did you want to be “when you grow up”?
I wanted to work in movies. Not necessarily as an actor, but to be involved in the industry in some capacity.