Experience matters when it comes to ensuring subsea cable systems survive variable ocean conditions. After all, if any part of the cable system assembly fails at sea, repairing or replacing it is expensive and arduous. PMI’s cable testing and analysis is an excellent way for customers and third parties to feel confident about their cable system components and the integrity of the complete system.
“Few labs offer the tests or use the equipment we do to find vulnerabilities and confirm satisfactory performance before the cable is deployed,” says Jay Marino, P.E., PMI Manager, Engineering, Government Services & Test Lab. “We’ve worked with many customers over four decades to simulate at-sea conditions and provide quality inspection and assurance services. PMI’s insight into a product’s durability is a value-added service that customers seek out. They like the fact that our tests can be uniquely tailored to meet their needs.”
As deep ocean exploration has grown over the years, the heavy-duty cables used in subsea projects are expected to last for decades. Unfortunately, 80% of unexpected challenges and delays in marine projects are caused by cable failure.
Equipment provides extensive measurement capabilities
Determining the service life of a cable system and/or its components is a specialty of PMI’s. Besides the tests PMI does on its own products, organizations come to PMI for certification and testing services, particularly ones designed to assess electrical, optical, and mechanical applications.
Customers with new cables may want to do tension cycling on them. PMI’s long span tension setup machine is capable of testing cables up to 457m (1,500 ft.) over multiple sheaves, with tension up to 53.4 kN (12,000 lbf.).
“A manufacturer that makes a cable assembly will send a sample to us to test,” says Marino, who has been involved with PMI’s cable testing facility for over three decades. “Important testing we frequently do for customers checks the cable’s subsea mechanical responses. When someone develops a new cable and wants to run it through its paces, we’ll do tension cycling on it. We’ll also measure the torque and rotation to verify its torque balance characteristics.
“Cables typically are ‘torque balanced,’ but that doesn’t mean they’re perfectly torque balanced,” he continues. “What it means is that the cable is typically designed to minimize torque. Some torque remains, sometimes a little or a lot.
“We can measure the torque that’s generated when it’s loaded. We can also measure its rotation,” he says. “For example, if we fix one end of a cable sample and pull on the other end while allowing it to rotate, we can measure that rotation. Or, we can fix both ends and measure the torque generated in the cable. We can also rotate one end to intentionally generate torque in the sample to see how it reacts. Of course, hydrostatic pressure testing is usually part of the picture. These are tests we typically run. There aren’t many test labs which have this type of equipment.”
The CBOS (cyclic bend over sheave) machine is used to check a cable’s subsea mechanical responses, including its fatigue resistance and simulating its handling system problems.
The equipment PMI uses to test and measure for performance and reliability include:
- Long span tension setup
- Hydrostatic pressure chambers
- CBOS (cyclic bend over sheave) machine
- 100-kip straight tension machine
The equipment can test:
- Raw cable (steel armored or synthetic strength member)
- Rope and hose assemblies
- Cable assemblies
- Cable hardware
- Terminations
- Other equipment used in subsea projects
Customer-driven laboratory testing
One of PMI’s hydrostatic pressure chambers (above) can be used to simulate at-depth pressure loading and verify seal and electrical and optical performance.
Each test is based on the customer’s unique set of parameters. Additionally, the time involved varies based on the customer’s application, interface, and materials requirements.
“We test the cable or component at the conditions that the customer expects during operations in the ocean,” says Thom Bosch, PMI lab technician who has been involved with the company’s laboratory testing for 14 years. “For example, if they’re towing a cable or component through the water, they can calculate the drag force on the towed object, which is related to the tension in the cable. We’ll test to that tension value plus a safety factor for dynamics, usually doing many cycles over hours or days. Our customers typically have an idea of how much variability they can tolerate and still operate their cable system or device.”
These kinds of customer-focused interactions are one reason PMI has been a leader of in-house dynamic cable testing and analysis for nearly 40 years.
The 100-kip straight tension machine is used to measure up to 65 feet of cable to determine its proof, tension and breaking strength.
“We offer independent testing services to any company in the industries we serve,” Marino says. “We can test the performance, and sometimes the limits, of a customer’s cable or equipment beforehand so that there aren’t any expensive surprises in the field.”
To set up a free consultation or get technical support, contact Jay Marino at jmarino@pmiind.com or any member of our leadership or sales team. Their contact information is found on the Contact Us page on our website.
In case you missed it, we’ve moved–and the PMI team is settled into our new home!
Housed at our previous facility since PMI’s inception in 1984, it was time for an upgrade. We’re now located at 990 Resource Drive, Cleveland, Ohio 44131, U.S.A., just 7 miles away from the old facility.
The new state-of-the-art facility provides increased production and testing space, improves process flow, and allows for the growth of customized cable engineering solutions.
“By moving to the new facility, we’re able to better meet the needs and requirements of our customers,” said Bob Centa, President. “For instance, our production flow is better suited to meet the trends in the industries we serve, improving productivity and efficiency in handing large cable reels.”
Other benefits of the new facility include:
- Expansion of PMI’s design, manufacturing, and testing capabilities that will dramatically improve operational efficiencies.
- Increase product and service offerings to PMI’s customers.
- Expand PMI’s geographic reach.
We’re excited about this new chapter and we’d love to share a bit of the transition to our new space with you through the pictures below.
We are proud to announce that after an external audit, the Quality Management System of PMI Industries, Inc. has been assessed and approved by Smithers Quality Assessments, Inc., to the following quality management system standard and requirements: ISO 9001:2015.
This certifies that our Quality Management System is applicable to design, manufacture and distribute offshore, subsea cable hardware assemblies, and provide testing services. Which demonstrates our commitment to our Quality Policy Statement:
PMI Industries, Inc. provides offshore, subsea cable hardware and assemblies that increase efficiency, reduce failures, and improve installation and deployment time. We are committed to meeting customer expectations, and all applicable requirements, through continuous improvement of our processes. Our advantage is delivering quality, on-time and cost-effective products and services.
Since 2017, PMI has partnered with Smithers Quality Assessments, an accredited quality and environmental management systems certification body, to achieve certification.
“This certification reflects our longstanding commitment to quality, continuous improvement, and our customers,” said Bob Centa, President of PMI Industries, Inc. “It demonstrates the significant effort by the PMI team to continue to uphold the ISO standard throughout the company.”
PMI, celebrating a history of 39 years in 2023, is a global leader in engineered solutions for underwater marine cable connectors and terminations, including assemblies and hardware. The solutions that PMI designs, manufactures, and tests are used on cable systems for impact and abrasion protection, to prevent bending and provide strain relief, and for dynamic and static cable protection.
Our products include high-strength cable terminations and gripping products, towed array and seismic survey lead-in and umbilical terminations, and suspension cable assemblies and hardware.
Our engineered subsea cable hardware assemblies are designed for the following:
- US Navy & Defense Contractors
- Oil & Gas
- Marine & Seismic Survey
- Ocean Exploration & Research
- Offshore Wind, Wave, and Tidal
- University and Research Institutes
State-of-the-art facility provides increased production and testing space, improves process flow, and allows for growth of customized cable engineering solutions.
Cleveland, OH, USA, December 15, 2022 – PMI Industries, Inc., a global leader in engineered solutions for underwater marine cable connectors and subsea cable terminations, moves to a new, state-of-the-art facility in January 2023. The move increases production and testing space by more than two-thirds, removes manufacturing constraints, and improves capabilities, resulting in better lead times and inventory control.
“We are excited for the next chapter in PMI’s history with this modernization of our production and office spaces,” said Bob Centa, President. “We are expanding our design, manufacturing, and testing capabilities and expect to dramatically improve our operational efficiencies. The move positions us to grow in the industries we already serve, increase the product and service offerings to our customers, and expand our geographic reach.”
The new facility offers room for a streamlined process flow that will impact many aspects of PMI’s operations, including access to tools and equipment, material handling, and other logistics improvements. Increased space also benefits PMI’s in-house dynamic cable testing and analysis, a value-added step among the capabilities PMI offers. Many at-sea conditions can be simulated by PMI through its testing, which is used to find cable system vulnerabilities or confirm satisfactory performance before the cable is deployed. In-house testing is available as an independent service to third parties, as well as to the industries PMI serves: oil and gas; marine and seismic survey; naval and military; offshore wind, wave, and tidal and sustainable renewable energy; ocean exploration and research; and university and research institutes.
According to Centa, the across-town move will not adversely impact PMI employees, allowing the company to maintain access to its current talent pool and attract new employees to accommodate growth. Additionally, the larger facility, located at 990 Resource Drive, Cleveland, Ohio 44131, U.S.A., offers easy access for delivery and pickup due to its proximity to major highways.
About PMI Industries, Inc.
PMI, celebrating a history of 39 years in 2023, is a global leader in engineered solutions for underwater cable connectors and terminations, including assemblies and hardware. The solutions that PMI designs, manufactures, and tests are used on cable systems for impact and abrasion protection, to prevent bending and provide strain relief, and for dynamic and static cable protection. Its products include high-strength cable terminations and gripping products, towed array and seismic survey lead-in and umbilical terminations, and cable assemblies and hardware. Industries served include: oil and gas; marine and seismic survey; naval and military; offshore wind, wave, and tidal and sustainable renewable energy; ocean exploration and research; and university and research institutes. For additional information, visit www.pmiind.com.
Ongoing improvements in 3D printing are helping PMI explore new ways to provide engineered solutions that meet customer needs. PMI is improving quality control, prototyping crucial components, and experimenting with designs that will reduce assembly time by taking advantage of 3D printing’s additive manufacturing technology.
“The PMI engineering team has used additive manufacturing to make solid three-dimensional objects from a CAD (computer-aided design) file for several years. Because fabrication materials are improving and becoming more cost-effective, we are investigating more ways we can apply the technology,” says Terrence Mathis, PMI Manager, Engineering-Cable Protection.
Engineering team members are managing small projects to improve mold fabrication, potential part casting, compression dam manufacturing, and more.
Analyzing tolerances and variations to improve quality assurance
PMI is using 3D printing to test engineering tolerances of manufactured parts, such as plugs and rings used in a variety of applications. The time needed to measure internal and external features of parts, and ensure their proper fit, can add hours to the quality control process and affect product yields. Also, it can add time-consuming iterations to production if changes occur late in the design cycle.
“Some complex parts have over 20 features that can take four or more hours to inspect,” Mathis says. “Different tools may be needed to measure each section. Depending on the production quantity, it can add a lot of time. Through tolerance optimization, PMI has the potential to improve manufacturing time and reduce cost.”
Prototyping components that customers need to remain operational
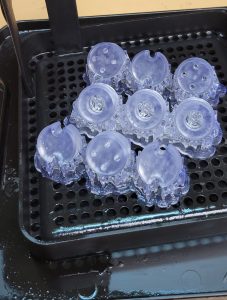
PMI is using 3D printing capabilities to prototype crucial components, such as its precision precast compression dams used in DAM/BLOK™ electrical splice kits.
Many of PMI’s field-installable products incorporate helical gripping rods as part of the kit. At times, it is necessary to reterminate a PMI product—sometimes while out on the ocean–to replace helical rods affected by excessive corrosion, or to refurbish the cable connector.
PMI manufactures the DAM/BLOK™ electrical splice kit as a full-ocean depth pressure splice for cable connections. However, there are over 100 existing DAM/BLOK electrical splice kit designs, not including splice kits that can be custom designed for customers. Despite the degree of customization, each kit includes several crucial components, including precision precast compression dams.
Currently, PMI is testing compression dams to ensure it prevents outside seawater as well as leak water within the cable from passing through the splice to the electrical connection. This is especially important at increasing ocean depths.
Developing designs that reduce assembly time
Customers who purchase PMI’s DYNA II cable hangers benefit from its tool-free installation and multiple degrees of freedom, which allow spreader rope loads to pass through with minimal effect on the lead-in and umbilical cables. Like many PMI products, DYNA II can be custom engineered into several configurable kits and accessories.
A collar assembly is just one of the components in a typical DYNA II configuration. PMI is using 3D printing to develop a new standardized collar to be used on legacy and new systems. The prototype collar is 3D printed in a wax resin, which is then cast in stainless steel. The collar serves a build-measure-learn function while saving tooling costs as PMI works to create an improved collar that benefits its customers.
Thinking outside the box to increase development speed
“Our customers turn to us for engineered solutions that include design, fabrication, and testing of subsea tow cables, hardware, assemblies, and protection,” Mathis says. “With a 3D printer, we’re able to take advantage in low-volume situations to revolutionize our development, design and replacement parts in ways that benefit our customers.”
Mr. Centa succeeds Bob Schauer who is retiring after 17 years of service
Cleveland, OH, USA, January 4, 2022 – PMI Industries, Inc., an engineering, manufacturing, and testing company with a global presence servicing energy, both fossil fuel and renewables, marine, research, and government industries announces the appointment of Robert (Bob) J. Centa, MBA to president. Mr. Centa succeeds Bob Schauer who is retiring after 17 years of service to PMI. Mr. Centa was most recently the Chief Financial Officer of The Great Lakes Brewing Co. in Cleveland, Ohio.
“Working at PMI has been truly rewarding and I will miss the daily interactions with the team,” comments Bob Schauer. Mr. Schauer started at PMI with a focus on turning around an underperforming company. As president, he led the company through the oil boom and bust cycles, established an overseas office, all while growing the business during the Covid crisis. “I look forward to spending more time with my family, traveling with my wife, woodworking, volunteering at community organizations, and writing,” comments Mr. Schauer. Speaking on the retirement of Mr. Schauer, PMI Industries board chairman Scott Eucker comments, “The PMI family will miss Mr. Schauer not only from a leadership and inspiration perspective but as a friend. I thank him for all his tireless efforts and wish him joy and happiness in his retirement.”
Mr. Centa brings a broad business acumen and over 25 years of experience in leadership, strategy, operations, and finance in manufacturing and distribution, as well as a wide range of industries and companies as diverse as start-ups, family-owned, private equity, and large publicly traded. Mr. Eucker comments, “I am excited to welcome Bob to the team. His broad business experience and previous leadership roles will be an asset in our company’s growth.” Mr. Centa earned a Master of Business Administration from Cleveland State University and a Bachelor of Business Administration from the University of Cincinnati.
About PMI Industries, Inc.
PMI, celebrating a history of 38 years in 2022, specializes in designing, manufacturing, and testing underwater cable hardware and assemblies. Servicing energy, both fossil fuel and renewables, marine, research, and government industries, PMI builds quality terminations, as well as supplies stoppers and cable grips, umbilical hardware, seismic and cable protection systems. Over many decades we have earned a global reputation for providing the right products at the right time, which ultimately reduces costs by increasing productivity and equipment service life. For additional information, visit www.pmiind.com.
For undergraduates from the Cleveland area, the Emerging Scholars Program offers a path to excellence
In the spring of 2011, a few weeks after he had accepted an offer of admission to Case Western Reserve, Terrence Mathis (CWR ‘16) opened a letter from a faculty member he had never met.
Stephen Haynesworth (GRS ‘87), an associate dean in the College of Arts and Sciences, had written to congratulate Mathis and assure him that he had made the right decision. “When we at CWRU admitted you to the university,” Haynesworth told him, “we demonstrated our respect for your achievements and our confidence that you can succeed here.”
Blog Summary:
- 80% of unexpected challenges and delays in marine projects is cable failure.
- Cable failure creates risks for losing expensive subsea equipment.
- Full-strength underwater cable terminations prevent cable failure during deployment and retrieval of subsea equipment.
- Unlike other helical terminations, PMI’s grips are built to hold your subsea cable to the full-rated breaking strength
- A benefit of the helical wire design permits easy installation of the termination anywhere along the length of the cable and does not require access to the cable end.
- Can be easy installation anywhere along the length of the cable and anywhere in the field.
- Do not require tools or cable preparation.
More subsea projects are happening than ever before, and ROVs, side-scan sonars, and other offshore equipment are almost always an element within them.
When equipment like ROVs and side-scan sonars are deployed or received, the twisting and bending of the cable at the termination point is common. Side-scan sonars and ROVs need these cables to stay intact and be able to bear the weight of the equipment. If these cables can’t keep up, it will cost serious delay and expense to projects.
Cable failure is the cause of 80% of unexpected challenges and delays.
The most common instance happens when subsea equipment is deployed from a vessel or retrieved from the sea and fails due to an extreme amount of tension being placed on the attached subsea cables. If these delicate cables are not terminated properly, they experience damage from strumming and snap loading. At this point, your crew can find themselves spending a good day starting over with installing a brand new termination – costing your project valuable time and money.
Without a proper underwater cable termination or grip, all of the stress and tension is concentrated along the cable where it is attached to the equipment. This is a ton of localized stress on what is usually a very expensive mechanical, electrical, or optical cable. Without a full-rated strength termination, you could be creating a recipe for disaster – cable damage, or worse, a cable break that results in the loss of expensive equipment.
How Helical Terminations Prevent Cable Damage
Helical terminations are designed to function similarly to a Chinese finger trap — a childhood toy that is a woven paper tube letting you place a finger into each end, and then, as you try to pull your fingers out, the tube tightens around your fingers. The harder you try to pull, the tighter the tube grasps your fingers, creating a secure hold.
Helical terminations work the same way. Helical rods are wrapped around the subsea cable at the termination location of the undersea equipment. With a helical termination, all of the stresses that would occur at one localized point on the cable are spread out over the length of the cable wrapped with the helical rods; therefore, greatly reducing the stress on any specific location of the cable.
To be technical, axial loading, a force that passes through the center of an object, causes elongation of the helix (or cable) and results in radial contraction. This compressive force gives the helical rods its ability to hold force. If you hold one end of the helical rod and attempt to pull the cable out, you transfer the load from the cable to the helical rods.
If at any point the load increases, the holding force increases. This mechanism provides a gradual transition of the load from the cable into the helical rod until the helical rods carry the full axial load.
Creating Reliable Attachment Points
A benefit of the helical wire design permits easy installation of the termination anywhere along the length of the cable and does not require access to the cable end. Many times attachment points are needed along the length of the cable. A good example of this is for creating an attachment point for the cable to be lifted from the seabed.
Why PMI’s Helical CABLE-GRIP™ and STOPPER-GRIP™ Terminations are a Preferred Choice
Unlike other helical terminations, PMI’s grips are built to hold your subsea cable to the full-rated breaking strength. When you are working with some of the most advanced and extremely expensive machinery in the industry, you can be confident that PMI’s equipment protects yours better than any cable hardware on the market today.
PMI’s Helical Terminations:
- Generate full-rated breaking strength.
- Permit easy installation anywhere along the length of the cable and anywhere in the field.
- Do not require tools or cable preparation.
- Come furnished in galvanized steel. Other materials, such as stainless steel, are available upon request.
- Work with many jacketed and synthetic strength members.
Invest in your project’s future
PMI’s Cable Grip and Stopper Grip Terminations are an inexpensive investment for preventing damaged cables or replacing a lost piece of expensive robotics. PMI underwater cable terminations have been used on cables for over 50 years, preventing subsea cable damage and maintaining cable integrity.
Check out our Full Rated Strength Terminations:
PMI offers Cable-Grip, Stopper-Grip, and EverGrip Terminations that all utilize Helical Rods.
Not sure what your project needs or have more questions about our helical terminations? Ask one of our experts today to help.
With more than 95,000 miles of shoreline, the United States looks like an ideal candidate for offshore wind energy development. But it’s not that simple.
A substantial portion of U.S. shoreline tracks the Southern Atlantic states and the Gulf of Mexico, where the winds are either too weak most of the year or potentially catastrophic during hurricane season. The Pacific Coast has steady, powerful winds, but the continental shelf drops off sharply near the shore, requiring floating wind-power platforms that cost much more than fixed-position wind farms.
The economics of offshore wind present a second order of complexity. Offshore wind developers have to weigh factors including:
- Costs of competing energy sources like coal and natural gas
- Population density of the area using the power
- Availability of subsidies and renewable energy credits
- Expense of designing, manufacturing, and deploying wind farms
An intriguing study from the Berkeley Lab’s Electricity Markets & Policy Group developed a series of models to compare the economic value of offshore energy projects along the Eastern Seaboard of the United States from 2007 to 2016:
“The market value of offshore wind between 2007-2016 varies significantly by project location and is highest for sites off of New York, Connecticut, Rhode Island, and Massachusetts,” the study found.
States with most promising developments
In a May 2018 article, POWER magazine listed the most promising states for offshore wind. That roundup included:
- Massachusetts. With the doomed Cape Wind project finally out of the picture, the prospects for other offshore power projects are improving. The state government has passed legislation targeting 1,600 MW of offshore wind power by June 30, 2027. The law requires a buffer of 10 miles between offshore wind farms and inhabited areas to avoid angering the public, which prizes its coastal views. Three companies are bidding for projects off Martha’s Vineyard.
- Maryland. Two companies have been awarded renewable energy credits to develop wind farms of 120 MW and 248 MW. The credits are worth $3.6 billion over two decades. Developers are required to create nearly 5,000 jobs and invest in a steel fabrication plant and port upgrades. The project will involve 77 turbines from 12 to 21 miles offshore.
- New York. Gov. Andrew Cuomo would like to see 2,400 MW of offshore wind power developed in the next two decades. He wants to start with 800 MW in 2018-19.
- New Jersey. The state’s Offshore Wind Economic Development Act, passed in 2010, sets a goal of 3,500 MW of new power generation by 2030. The state’s Board of Public Utilities plans to solicit 1,100 MW of new projects, which would be the nation’s largest so far.
States and projects further down the coastline in Georgia and the Carolinas appear much less likely to bear fruit, the POWER magazine article explained.
Pacific Ocean possibilities
The Pacific Coast and the Hawaiian Islands each present intriguing opportunities because their terrain limitations require innovations in floating offshore platforms. Unlike Europe’s North Sea and the Eastern Seaboard of the United States, the shoreline of the Pacific plunges to depths that are impractical for the development of standard offshore wind turbines mounted on the seafloor.
In May 2018, the U.S. Navy complicated matters even further, stating that vast swaths of California coastline — including all of Southern California — should be off-limits to wind farms because the Navy needs that space for national defense purposes, the Los Angeles Times reported. The Navy cannot decide where wind farms will be deployed, but it has considerable influence.
Perhaps the best news for the Pacific comes from the coast of Scotland, where the first floating platform offshore wind farm is up and running. That wind farm is proving to be remarkably energy efficient, using up to 65% of its capacity factor, which is far better than land-based gas and coal power, according to Greentech Media. Capacity factor estimates a powerplant’s output as a percentage of its theoretical full energy output.
With the cost of developing offshore wind farms falling rapidly and floating platforms showing promise, power from the Pacific might be closer to reality than many observers suspect.
Great Lakes
A wind farm project in the works near our home base in Cleveland will test the viability of the Great Lakes, which have ample wind, high population densities, and relatively shallow water.
The Icebreaker project plans to deploy six turbines in Lake Erie about 8-10 miles northwest of Cleveland. Supporters hope this pilot project becomes a catalyst for further development throughout the Great Lakes.
Offshore wind is coming to U.S. shores
Many coastal states have ambitious renewable-energy goals that will require the development offshore wind because there’s only so much they can do with solar, land-based wind, and biofuels. Fortunately, they can benefit from decades of European experience in offshore wind combined with steep declines in development costs.
U.S. wind projects also raise the prospect of bringing good-paying jobs and economic development to communities that need a boost after declines in their manufacturing base.
As a manufacturer of premium cable accessories for offshore wind and other marine-energy projects, PMI is doing its part to support the industry and help reduce our reliance on fossil fuels. We believe the United States is ready for offshore wind, and judging from the volume of new projects in the pipeline, we’re not alone in that assessment.
Related articles:
America’s First Offshore Wind Farm Is Finally Ready for Prime Time
Why the U.S. Should Embrace Offshore Wind
How Ice Could Impact Subsea Cables and the Great Lakes’ Offshore Wind Success
The Cable Challenges of Saltwater vs. Freshwater for Offshore Wind Projects
The challenges of developing practical, economical offshore wind power are pushing engineers and entrepreneurs to new heights — and depths — of ingenuity.
We’ve talked about the pitfalls and potential of offshore wind and other marine renewables for years in our Ocean Engineering Blog. We’ve noted that it’ll never be easy to build technologies that must be submerged in corrosive, turbulent subsea environments. And marine-renewables will remain a tough sell as long as oil prices stay low.
But these challenges haven’t stifled innovation in the ocean-renewables sector, especially offshore wind. Here’s a look at some of the encouraging news we’re seeing:
Autonomous underwater and remote-operated vehicles (AUVs, ROVs)
The cost of deploying ships and divers to inspect, maintain, and repair cables and other subsea components has been a costly drag on offshore wind farms for decades. Widespread adoption of versatile, low-operating-cost AUVs and ROVs can reduce those costs substantially.
As we learned at Subsea Expo 2018 in Aberdeen, Scotland, companies developing advanced AUVs and ROVs are adding new capabilities that, for instance, add a cutting tool to an inspection AUV. Another promising development is underwater charging stations that allow subsea vehicles to roam free without cables. Instead, the stations themselves have cable connections to power sources.
Larger, more powerful turbines
GE Renewable Energy’s forthcoming Haliade-X 12-mw turbine underscores the drive to build ever-larger devices that produce more energy in a single tower. Billed as the most powerful turbine on the planet, the Haliade-X will be able to power 16,000 European households with a single turbine. That means a single wind farm of 50 towers could serve 800,000 households — potentially a city of more than 2 million people.
Standing 260 meters high with a 220-meter rotor, the Haliade-X will produce 45% more energy than any other turbine on the market, GE says. It’s expected to start showing up in wind farms in 2021. For more on the size challenges in offshore wind, see this profile of former Siemens CTO Henrik Stiesdal in Wind Power Monthly.
Floating platforms
The prospects for offshore wind farms on floating platforms got a boost in March 2018 when Statoil announced its new floating platform off the coast of Scotland reached a 65% capacity factor for November 2017 through January 2018 — besting a host of competing power sources. That news supports the principal rationale for floating platforms: deploying them farther from shore, where the winds are stronger and more consistent.
Capacity factor estimates a powerplant’s output as a percentage of its theoretical energy capacity. Greentech Media noted that U.S. onshore wind farms have a capacity factor of 37%, while coal- and gas-fired power plants have capacity factors of 54-55%.
Suction-bucket foundations
Floating platforms could be the future of offshore wind, but most projects in the next few years will keep using towers anchored to the seabed. Current anchoring methods create an abundance of noise, disturbing sea life and generating concerns about the environmental impact of offshore installations.
A new alternative is the suction-bucket foundation, which uses a base shaped like an inverted bucket. It works like this: After the bucket settles on the seafloor, operators pump out all the water inside it, creating a pressure differential that helps fix the bucket in place. When it’s time to decommission the bucket, water can be poured back into it. The first commercial-scale suction-bucket foundation in a wind farm was installed earlier this year off the coast of Scotland, Powermag.com reported.
Research updates
Here’s a look at recent research in the offshore-wind sector:
- Seabird avoidance. Seabirds have little trouble avoiding the spinning blades of offshore-wind turbines, a new study finds. Windpower Engineering & Development summarized results of the Bird Collision Avoidance Study, which used video cameras and high-tech sensors to track bird movements around a working wind farm in the English Channel. The study analyzed more than 600,000 videos monitoring activity at the wind farm. Of those, about 12,000 showed bird activity. Notably, the videos captured a scant six collisions over the course of the study.
- Anti-corrosion studies. Offshore Wind Journal reviews reports pointing to potential solutions to the nagging problem of corrosion in subsea environments. The reports estimated that reducing corrosion could generate savings in the tens of billions of dollars throughout the ocean-renewables sector over the next three decades.
Offshore wind keeps showing more promise
These updates offer just a glimpse of the encouraging developments in the offshore-wind sector. As turbines grow more powerful and engineers figure out new ways to reduce costs and protect subsea ecosystems, it will become ever more realistic to depict offshore wind as an experimental power source with mainstream potential.
Related articles:
Innovations Shrink Offshore Wind Timelines
Artificial Island Sparks Innovation In Wind Energy
Pros and Cons of Floating Platforms in Marine Renewable Energy